PEC's Single and Twin Arc Rotary Head Weld Cladding Systems
In the welding and fabrication industry, automated welding techniques are used to navigate the torch around the joint to be welded or surface to be weld-clad. Weld cladding of Oil & Gas industry wellhead products present problems due to components weighting up to and over 20tons and possessing complex shaped surfaces. In many multi-bore valve blocks, the bores that require overlay are often off-centre and non-circular. These features highlight the limitations of weld cladding with the conventional technique of rotating the component.
In 1998, PEC engineers made a major breakthrough in weld cladding technology by replacing the turntable altogether and rotating the torch on a 'Rotary Head' inside of a stationary component.
PEC Rotary Head systems are the benchmark in this technology and we are proud that all systems installed since its introduction are still in use today.
RTH - 1
These are some of the major benefits to the users of the PEC Rotary Head Systems:

... savings in manufacturing time
• Reduced time in centring the torch to the bore without moving the
component
• Reduced welding time using PEC's unique TwinArc TIG process (minimum
of 4" bores)
• Fast preheating of the component as there are no restrictions on the
number of heating pads that can be fitted to the stationary component
• Reduced welding time - rotational speeds up to 3rpm are possible with
low mechanical wear
• Rapid relocation of the torch to other bores on the component
• Components can be pre-heated prior to setup which reduces 'dead' time
... simplifies welding of
• Very heavy components
• Components that cannot be manipulated
• Non-circular bores and surfaces
• Valves with multiple offset bores
... produces higher quality weld overlays
• Smooth and stable rotation of the weld head results in smoother welds
finishes
• More consistent deposit of welds
• Lower defects due to use of more automation techniques
• Reduced risk of operator errors as many manual tasks have been
eliminated
• Total automation of difficult tasks
... improves health & safety of the welder
• Operator does not have to manipulate heavy components manually
• Operator is not standing on a rotating turntable whilst attending to the job
• Silent operation
... lower installation & maintenance costs
• Elimination of electrical preheat slip rings (required on turntables)
• Reduced mechanical wear in moving parts
• Reduced machine footprint means better utilisation of shop floor space

A - Column height
B - Boom length
C - Boom travel distance (Y axis)
D - Boom travel distance (X axis)
E - Base dimensions
F1 - Single Arc slide travel distance
F2 - Twin Arc slide travel distance
G - Maximum rotation angle
System Dimensions:
RTH AC Systems can serve multiple work stations with electronically controlled column rotation where switching between different jobs is much easier and more convenient, drastically saving operational time.
Key features of the Rotary Head Systems:
RTH - 2
10 reasons to choose a PEC Rotary Head Weld Cladding system,
please check this list before you commit to a purchase
• Automatic Torch Centering for bores and seal areas
• Automatic Racetrack-shape BOP bores
• Automatic Racetrack-shape BOP ring-groove and flat seal areas
• Tapered bores
• TwinArc Option for extra productivity
• Intersecting Cross Bores in Single and TwinArc
• Seat Pockets in Single and TwinArc
• Bore sizes up to 1400mm with no adaptors, extensions or turntables
required
• Bespoke job shapes
• Unlimited job weight
• Simple to use interface for fast and efficient job set-up
• Welding parameter and process-feedback monitoring
* Techniques and technologies used by our competitors.
1.
More than 15 years experience with Rotary Head systems installations
2.
Can weld bores up to 1250 mm diameter and 2500 mm height in one operation without using 'tricks' like 'bent' torches or mechanical extensions*
3.
Reliable electrical and water/gas services - we do not use unreliable rotary unions* & rubber seals for coupling cooling water and shielding gas to the rotating welding torch
4.
We use high quality precision ballscrews and guide rails on our Column & Booms not low accuracy rack* and pinions
5.
Choice of welding processes - Unique high productivity TwinArc™ TTIG & MIG capability
6.
HotWire TIG & Pulsed MIG processes running on the same system - unique to PEC
7.
Simultaneous NC operation in the horizontal and vertical axes for up to 2500 mm movement and 0.01 mm accuracy
8.
PEC's SynerTIG™ control systems for up to 150% higher welding rates compared to competitor systems
9.
A minimum of 10 years technological lifespan - our products are designed to be expanded and upgraded with any new functions developed. We have an evolutionary policy to product development and you benefit from it over time
10.
High quality references available from major companies like Cameron, FMC, and GE Oil & Gas (formerly Vetco Gray) worldwide group companies

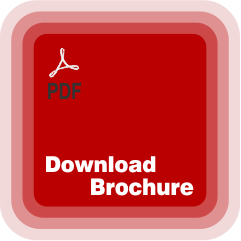
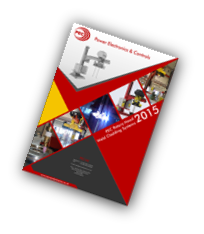
