Savings in welding time more than 50% when you use the TwinArc™ TIG process in bores from 4” (100mm) diameters
A significant cost saving technology available only from PEC
TwinArc™ TIG (GTAW) Welding Process
In order to increase TIG productivity for fusion and weld overlay of larger components, PEC developed the TwinArc™ Hotwire TIG process in which two torches are attached to the same weld head to produce two individual TIG arcs. The two arcs are positioned diametrically opposite and hence have little heating influence on each other. An important requirement in weld cladding is that the two arcs produce weld deposits with similar fusion levels, iron content and heat inputs. This is difficult to achieve as the flow of the weld pool in the vertical (2G welding position) is governed by gravitational forces and surface tension effects.
Our development of the SynerTIG™ arc control system was essential to the success of the TwinArc™ TIG process as it automatically adjusts welding parameters to equalise the weld deposits.
In application terms, the two arcs can be used to weld at the same or different levels (see schematics). With either method, the welding time is reduced by up to 50% in bores greater than 4" (100mm).

TwinArc™ TIG
• Metal deposit rate between 2.75 to 3.3kg/h for
TwinArc TIG
• Metal deposit rate between 4.0 to 6.0 kg/h for
TwinArc MIG
• Local heat inputs similar to single arc operation
• Simultaneous welding of first and second layer
halves welding time
• Reduced distortion of components
• Welding time reduced by 35 to 50% (TIG) and
77 to 80% (MIG) compared to single arc hotwire
TIG
In 2004, as a further development of the TwinArc™ concept, PEC developed the TwinArc™ MIG process which has approval for use on well head valve overlay applications and is accepted by a number of oil companies. Several of the single and TwinArc™ versions of the SynerMIG™ systems have now been installed. In bores greater than 4 ", welding times have been reduced to less than 30% of that achieved with SingleArc hotwire TIG. All welding is done in a single pass and meets the required metallurgical and mechanical requirements for weld cladding.
The TIG & MIG processes can be fitted to all our Rotary Head and Conventional weld cladding systems offering the advantages welding small bores (1.5") using TIG and MIG for single layer high productivity welding of larger bores.
Application of the TwinArc™ TIG Process
Weld cladding of valve bodies.
The requirement is usually to inlay the internal cavities of well head valves with a corrosive and wear resistant material. In order to achieve the welding and mechanical specifications, a two layer approach is required. This can be time consuming as the bore has to be welded 'twice'. A more efficient method is to weld the two layers in a single pass using the TwinArc process. The two arcs are initially set to be at the same vertical level to produce a short length of weld together. The two torches are then driven into an 'offset' position as shown with Torch #1 producing the first layer and Torch #2 the second layer. No interlayer cleaning is necessary as the bore is immersed in Argon gas all the time. For bore diameters > 4", typical reductions in arcing time of between 40-50% are possible - a considerable saving in cost. The 'offset' method is generally used on smaller (4") bores to prevent localised heat build-up. With larger bores, a two layer techniques is preferred with both torches positioned at the same level.

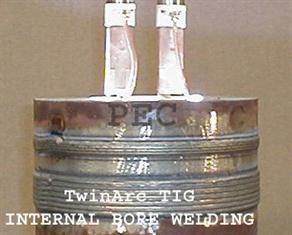
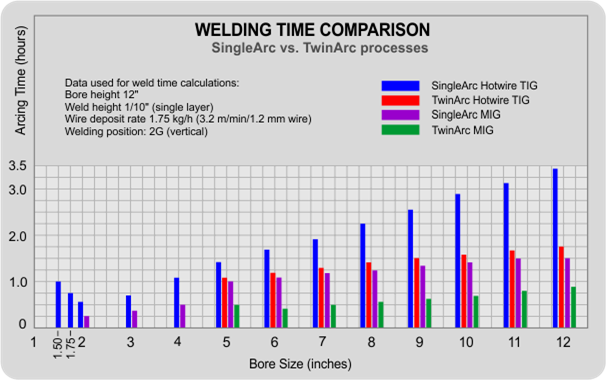
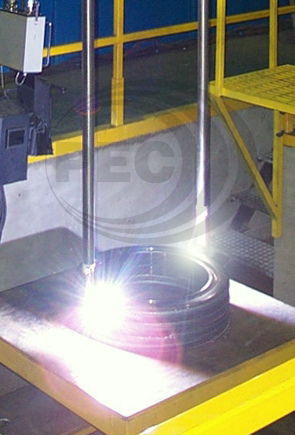
• Minimum bore size 100mm (4")
• Maximum size 1450mm
• 2G (vertical) welding position
• Simultaneous cladding of internal and external
surfaces
• Independent controls for both arcs
• System process easily switched between
SingleArc and TwinArc welding as desired
• Same layer welding or first/second layer
simultaneous overlay as desired
• Synchronisation of arc parameters for both arcs
resulting in greater consistency of the two weld
deposits
• Uses same welding procedure as single arc
process
• Proven technology
Features of the TwinArc™ processes
Benefits of the TwinArc™ processes